Special Report - Batteries: Powering the Future
Much of the investor and financial press focus has been on the ongoing battle in the semiconductor space, but the game afoot in the battery space is equally important. Virtually every electronic device, appliance, and vehicle around you contains both semiconductors and lithium-ion batteries. Batteries are also a key input in both the energy and transportation transitions, as well as the ongoing push for increased automation. There’s much more here for the investor than meets the eye.
In the investment world, the battery story is focused on Electric Vehicles (EVs), the related commodities and Elon of course. In the mainstream media and in government circles, the focus is on the sudden realization of China’s dominance in this key strategic area, and a reactionary swerve into national industrial policy and geo-strategic machinations by think tanks and governments in both the US and Europe. Let us, however, focus on the “here and now” and explore the current trends in the following 3 areas: Battery demand drivers, the current supply chain, and the geopolitical shifts that are underway. Then we will round it out by diving into the resulting investment opportunities in the space. So, turn on the espresso machine, get ready to make a few, and recharge your batteries - here we go!
EV demand is in the driving seat
Lithium-ion batteries have 3 primary demand drivers: consumer electronics, energy storage, and transportation. While consumer electronics were the initial driver of the commercialization, and demand for batteries from this area is set to more than double in the decade between 2015 and 2025, energy storage and transportation are the main drivers now and in the future.
Sales of EVs broke new records in 2021, with nearly 10% of global car sales being electric, four times their market share in 2019. Public and private spending on EVs doubled relative to 2020. Five times as many more EV models were available in 2021 relative to 2015, and most major carmakers are announcing plans to further accelerate electrification of their fleets. China accounted for half of the growth of the EV market in 2021, with more vehicles being sold in China in 2021 (3.3 million) than in the entire world in 2020. Sales in Europe continued to grow robustly (up 65% to 2.3 million) after the 2020 boom, and they increased in the US as well (to 630 000) after two years of decline.
Global battery demand doubled in 2021, driven by electric car sales in China
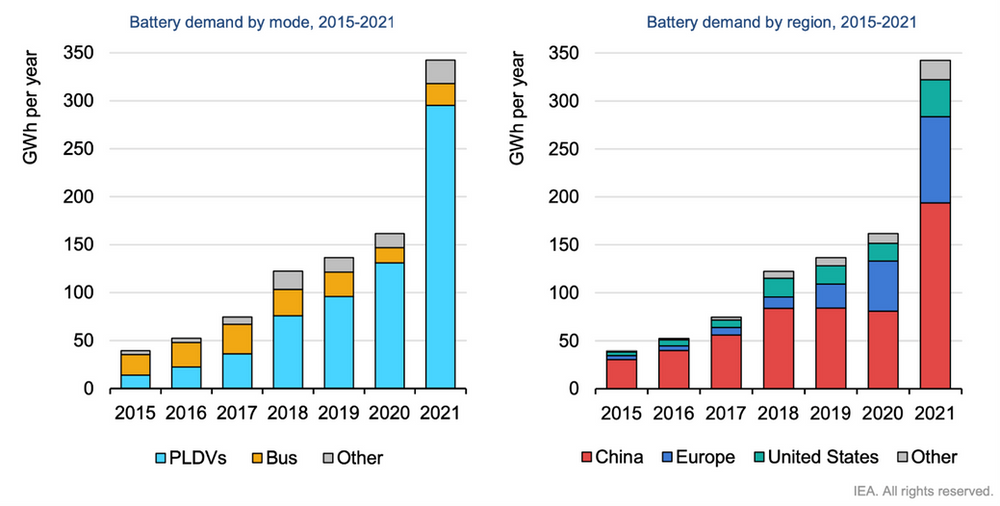
Notes: Gwh=gigawatt-hours; PLDVs=passenger light-duty vehicles; other includes medium- and heavy-duty trucks and two/three-wheelers. This analysis does not include conventional hybrid vehicles.Sources: IEA analysis based on EV Volumes.
Unsurprisingly, battery demand for EVs doubled in 2021, according to the IEA. This surge is driven by the increase in electric passenger cars, but battery demand for other transport modes, including medium- and heavy-duty trucks and two/three-wheelers, also increased by 65%. China experienced unprecedented growth and accounted for the largest share of automotive battery demand, with almost 200 GWh in 2021, up 140% from 2020. Growth was also impressive in the US where demand more than doubled in 2021, albeit from a lower base. Europe’s demand growth was slightly lower than last year, yet it still increased more than 70%.
The current global (Asian) battery supply chain…
Today’s battery and minerals supply chains revolve around China. Chinese companies produce three-quarters of all lithium-ion batteries, and the country is home to 70% of production capacity for cathodes and 85% for anodes, both being key components of batteries. Over half of lithium, cobalt and graphite processing and refining capacity is located in China. Europe is responsible for over one-quarter of global EV assembly, but it is home to very little of the supply chain apart from cobalt processing at 20%. The US has an even smaller role in the global EV battery supply chain, with only 10% of EV production and 7% of battery production capacity. South Korea and Japan have considerable shares of the supply chain downstream of raw material processing, particularly in the highly technical production of cathode and anode material. South Korea itself is responsible for 15% of global cathode material production capacity, while Japan accounts for 14% of cathode and 11% of anode material production. South Korean and Japanese companies are also involved in the production of other battery components such as separators.
The EV battery supply chain
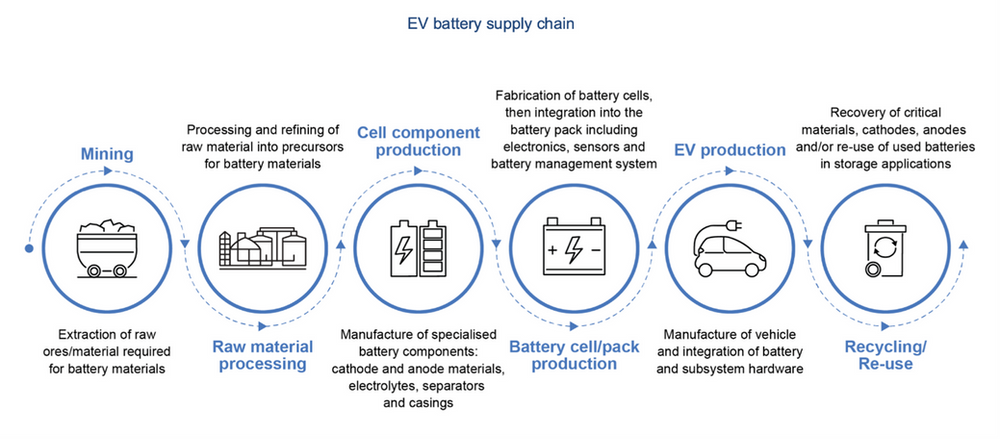
Source: IEA: Global Supply Chains of EV Batteries Report
Most key minerals are mined in resource-rich countries such as Australia, Chile and the Democratic Republic of Congo, and handled by a few major companies. Governments in Europe and the US have bold public sector initiatives to develop domestic battery supply chains, but the majority of the supply chain is likely to remain Chinese through 2030. For example, 70% of battery production capacity announced for the period to 2030 is in China.
However, while China clearly seems to be at the forefront on both materials and innovation, upon closer inspection, things are actually a little more nuanced. EV battery supply chains consist of multiple complex stages that are spread out around the world, from extracting the necessary mineral ores and refining to form sufficiently pure chemicals, to advanced synthesis processes to form cathode and anode materials. Similar complex supply chains can be found in other battery components such as electrolytes and separators. Cells are then fabricated and housed in modules within a battery pack which is integrated into the EV.
To understand current trends and future prospects of EVs, it is critical to understand all of the stages in this complex supply chain. Below we will explore the different components.
Mining
The five key battery materials are lithium, nickel, cobalt, graphite, and manganese.
Lithium is extracted from two very different sources: brine or hard rock. Lithium brines are accumulations of saline groundwater with high lithium contents and are typically located in the high elevation areas of Bolivia, Argentina and Chile in South America, with Chile being the largest producer. Brine deposits often contain large quantities of other useful elements such as sodium, potassium, magnesium and boron, which offsets some of the cost of pumping and processing brine. Lithium hard rock (spodumene) is primarily mined in Australia. Novel processes are being developed to extract lithium from unconventional resources such as geothermal brine. Currently, the top-five lithium suppliers account for about half of global lithium production. Major lithium suppliers include a mixture of large chemical and mining companies including Sociedad Química y Minera de Chile SA (Chile); Pilbara Minerals (Australia); Allkem (Australia); Livent Corporation (United States); and Ganfeng Lithium Co. (China). Unlike for other battery metals, lithium extraction companies tend to be specialized in lithium mining and chemical companies.
Nickel is found primarily in two types of deposit – sulphide and laterite. Sulphide deposits are mainly located in Russia, Canada and Australia and tend to contain higher grade nickel, which is more easily processed into Class 1 battery-grade nickel. Laterite, however, tends to contain lower grade nickel and is mainly found in Indonesia, Philippines and New Caledonia. Laterite requires additional energy intensive processing to become battery-grade nickel. Nickel production is less concentrated than lithium with about nine companies supplying half of global nickel production. Key nickel suppliers include: Jinchuan Group (China); BHP Group (Australia); Vale SA (Brazil); Tsingshan (China); Nickel Asia Corporation (Philippines); and Glencore (Switzerland).
Cobalt is predominantly mined as a by-product of copper or nickel mining. Over 70% of cobalt is produced in the Democratic Republic of Congo (DRC) and Glencore (Switzerland) is the largest global producer. Other key cobalt suppliers include: Jinchuan Group (China); CN Molybdenum (China); and Chemaf (DRC).
Graphite is the dominant anode material and can be found naturally or produced synthetically. Natural graphite mining is dominated by China (80%), though global production is becoming more diversified, with many greenfield graphite mining projects being developed in Tanzania, Mozambique, Canada, and Madagascar.
Manganese resources are more widely distributed around the world than the other battery metals and remain available at relatively low cost. There is a general expectation that there will not be an ore shortage in the near term. The leading producers of manganese ore include South Africa, Australia, Gabon and China.
Check out the full report below:
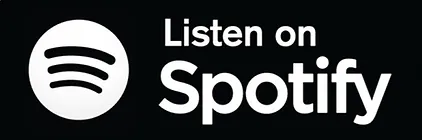